超声波发生器是一种将标准 50Hz 或 60Hz 输入电压转换为适用于驱动超声波换能器的高频输出电压的电气设备。调整输出电压的幅度和波形以满足超声波的要求。
电源复杂性
应用的瞬时功率特性分为四类(通常取决于负载类型),这在一定程度上决定了电源所需的复杂程度
- 恒功率。在负载循环期间,功率是恒定的。当负载相对恒定时会发生这种情况,例如雾化或气蚀。
- 可变但可预测的力量。功率在整个负载周期内以可预测的方式变化——即,从一个负载周期到下一个负载周期的功率变化是相同的。超声波插入就是一个例子。
- 可变但半可预测的功率。功率在整个负载周期中变化,但以半可预测的方式变化——即,总体功率趋势是相同的,但部件之间可能存在一些差异。例如,一些金属焊接部件可能具有较厚的氧化层或镀层,需要更多时间来擦洗。同样,一些塑料焊接零件可能有更多的脱模剂。
- 不可预知的力量。可以在大范围内预测功率,但无法预测瞬时功率。一个例子是超声骨切割,其中骨的成分随切割深度而变化,并且外科医生的应用不同(例如,施加的力的变化、刀片的扭曲或弯曲、润滑量等)。
共振型
必须指定电源以串联或并联谐振方式运行。(在某些情况下,可以指定中频。)这些谐振中的每一个都可能具有某些优点,但两者都在实践中广泛使用。无论选择哪种,换能器必须兼容(即,为串联谐振而设计的换能器在并联谐振时不能正常工作,反之亦然)。
主要要求
在某些情况下,宽带功率放大器可能适用于驱动超声波堆栈。但是,大多数专用超声波电源都具有某些可以提高性能的专用电路/软件。
自动调节
锁定初级共振
所有超声波系统都有一个初级共振(所需的工作共振)。此外,还会有二次(杂散)共振。当电源启动时,它必须锁定初级谐振而忽略次级谐振。
追踪初级共振
在超声操作期间,初级共振的频率可能会发生偏移。
- 随着电池堆温度升高(由于内部损耗或从负载传递的热量),频率可能会漂移得更低。
- 由于陶瓷的非线性,在大功率下频率可能会下降。
- 由于对负载的反应,频率可能会发生偏移。这种转变可以是积极的,也可以是消极的。例如,图1显示了在超声波金属焊接期间大约200Hz的频率下降 。
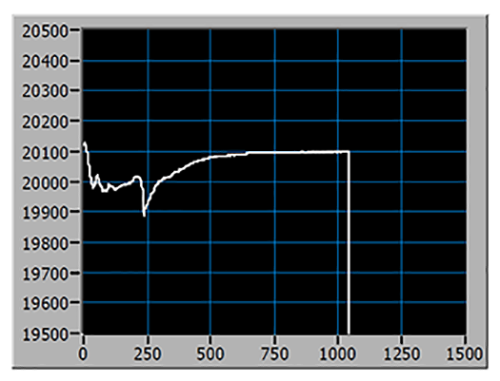
不管是什么原因,发生器都必须能够自动跟随这个频率偏移。否则,频率的微小变化将导致堆栈输出幅度的显着崩溃。这是因为超声波堆栈通常具有非常窄的带宽。例如,对于图2所示的 20kHz 换能器,根据驱动源突然断开时的幅度衰减测量结果确定了约 40 Hz 的开路带宽(即 Q 为约 500)。在这种情况下,共振频率偏移仅 20 Hz 将使换能器的幅度降低 30%,可用功率输出降低 50%(假设电输入恒定)。
当添加额外的堆栈组件(变幅杆 + 工具头)时,情况会变得更糟(Q 增加而带宽减少)。然后频率跟踪变得更加关键。但是请注意,在负载下,随着能量传递到负载,Q 可能会显着降低(即带宽增加)。
频率跟踪通常由锁相环 (PLL) 处理,其中电流和电压之间的相位角保持在恒定值。理想情况下,电流和电压将完全同相,以使负载看起来完全是电阻性的(即,没有无功分量)。然而,在实践中,这在高 Q(窄带宽)系统中可能是不可能的,因为频率的微小变化会导致相位的大变化。在这样的系统中,PLL 可能难以保持相位。在这种情况下,稍微异相的操作可以使 PLL 具有更好的性能。
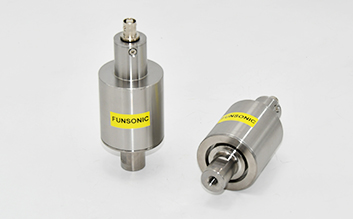
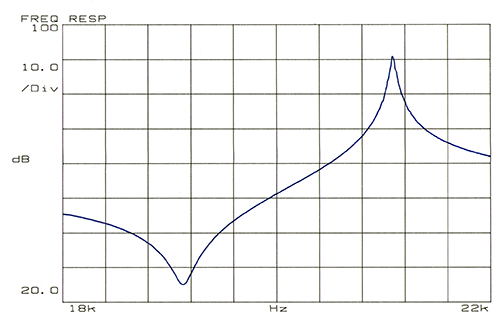
自动调整幅度
大多数应用可以通过控制输出幅度而不是功率来得到最好的控制。原因是功率是力和速度的乘积(其中速度与输出幅度有关)。因此,给定的功率可以通过低速的高力或高速的低力或介于两者之间的力来实现。尽管所有这些条件都可以产生相同的功率,但应用程序可能仅对其中一个做出最佳响应。因此,幅度应被视为独立(输入受控)变量,而功率通常应被视为因(输出结果)变量。
当堆栈在空气中运行(即空载)时,它将具有给定的输出幅度。这是规范。然而,在负载下,振幅趋于崩溃。在更高的负载下,振幅崩溃会更大。这类似于以固定油门位置行驶的汽车,汽车的速度在山坡上会降低——山坡越陡,速度降低的幅度越大。
发生器需要某种方法来监控堆栈幅度,然后根据需要调整幅度。这类似于汽车中的巡航控制,无论坡度如何,速度都保持恒定。
调谐电感
超声波系统的一个特点是即使负载是纯电阻性的,频率也会在负载下发生偏移。随着负载的增加,串联和并联谐振会相互靠近。在临界负载下,这两个共振收敛。在临界负载之上,系统不再共振。
为了克服这种情况,必须添加一个调谐电感器。为了在串联谐振下工作,调谐电感器与陶瓷并联(即跨陶瓷引线)。对于并联谐振操作,调谐电感器与陶瓷串联添加(即与一组陶瓷引线串联)。该电感器的阻抗应等于所有陶瓷的组合容抗。
次要要求
许多专用超声波电源具有保护系统的电路/软件。这可以包括防止接地故障、功率过载、过电压、过电流、过高的陶瓷温度和频率跳跃(从初级谐振到附近的次级谐振的跳跃)。
电路/软件也可用于监测或控制超声过程。例如,焊接锂离子电池时各种表面污染水平的功率。通过监测能量,可以确定焊缝的质量,并且可以拒绝有缺陷的焊缝。此外,可以控制能量输入以确保更一致的焊接,而不管诸如表面污染或其他不受控制的变量等因素如何。这个过程被称为“能量控制编程”或ECP。对于锂离子电池,Lee 将此最小能量设置为 800 焦耳。
lee将相对较薄的试样焊接在一起(0.4 毫米焊接到 1.0 毫米和 0.2 毫米焊接到 1.0 毫米)。对于具有显着横向尺寸的较厚材料,监测或控制金属焊接过程的能力更加困难。他说:“因此,我们发现仅了解 金属焊接系统的电气输入参数并不能消除焊接质量可变性和工具粘连等关键问题。 ” 然而,塑料焊接系统可能更适合这种监测/控制。